Rientro atmosferico e volo ipersonico: i segreti dell’innovativo cassone alare
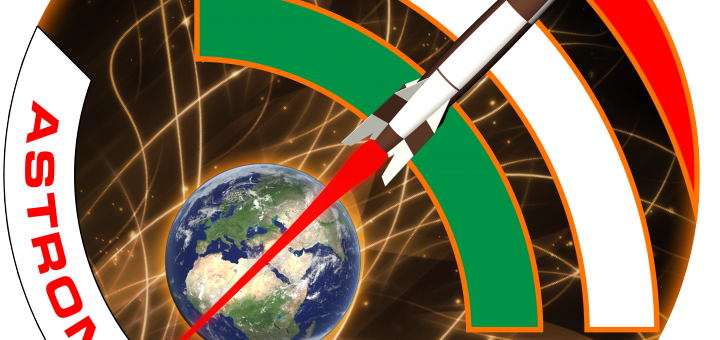
Intervista di dedalonews.it con Franco Fossati, dell’Advanced Projects – Transportation and Entry Systems di Thales Alenia Spazio Italia
Un innovativo bordo di attacco alare, refrigerato attivamente e in grado di resistere alle temperature di un rientro atmosferico, come pure a quelle di un volo prolungato a velocità oltre cinque volte superiori a quella del suono, piastrelle isolanti efficaci come quelle degli shuttle ma cinque volte più sottili, una innovativa struttura contemporaneamente termica e portante, un innovativa metodologia di calcolo e progettazione multi fisica e non lineare, strutture a deformazione controllata: è molto lunga la lista delle tecnologie messe a punto e sperimentate contemporaneamente con pieno successo nei giorni scorsi su un cassone alare sottoposto ad uno dei più lunghi e al più complesso test mai effettuato al mondo in un Plasma Wind Tunnel (PWT), con 15 minuti di accensione del generatore di plasma. Protagonisti, oltre il CIRA di Capua che gestisce il PWT, Thales Alenia Spazio Italia (capo progetto), il dipartimento di Ingegneria Aeronautica e Aerospaziale della Scuola di Ingegneria Spaziale dell’Università La Sapienza di Roma, il Centro Studi Materiali e altre aziende e centri di ricerca italiani. Il tutto, sotto il cappello del programma ASA (Advanced Structural Assembly) finanziato dall’Agenzia Spaziale Italiana (ASI).
Durante il test, del quale abbiamo già parlato, ma che oggi cerchiamo di approfondire nei suoi aspetti tecnici, è stato raggiunto e mantenuto per 15 minuti un flusso termico dell’ordine di circa 0,5 MW/m2 al punto di ristagno (dove l’aria si ferma picchiando contro il bordo di attacco, punto di massima sollecitazione). Se si considera che il tratto caldo della discesa delle capsule lunari Apollo aveva una durata di 5 minuti (anche se con un flusso termico maggiore per l’altissima velocità di rientro) e quello dello shuttle di 12, si può notare la gravosità delle condizioni imposte a materiali e tecnologie sottoposte alla prova nel PWT. In particolare, il bordo d’attacco ha un’elettronica interna commerciale che non poteva superare i 100°centigradi, con temperature esterne dell’ordine dei 1000°C.
Ne abbiamo parlato con Franco Fossati, dell’Advanced Projects – Transportation and Entry Systems di Thales Alenia Spazio Italia e responsabile tecnico di questo programma.
Su che tipi di aeromobile potrà essere usata, suborbitali, orbitali tipo shuttle, ipersonici?
Su tutti questi tipi. Infatti il test è stato effettuato considerando il flusso termico di un rientro da LEO, quindi quello di un rientro di un veicolo orbitale, che è la condizione più impegnativa, ed è durato 15 minuti.
Un record di durata mondiale per un test in galleria al plasma (PWT, Plasma Wind Tunnel)…
Si; avevamo previsto una durata anche maggiore, di 20 minuti, ma un problema tecnico ha suggerito di fermarci a 15 minuti. In ogni caso eravamo arrivati a regime e il test è quindi valido a tutti gli effetti per gli obiettivi che ci eravamo prefissati ed è risultato altamente significativo.
Abbiamo avuto lo shuttle, poi il Buran, che ha volato una sola volta, c’era Hermes, che si è fermato alla fase di studio. Rispetto alle tecnologie messe a punto per questi veicoli aerospaziali, una tecnologia come realizzata da voi, quanto è innovativa e che tipo di salto in avanti può consentire?
I salti in avanti sono molteplici. Prima di tutto le varie parti sono smontabili e rimontabili direttamente dall’esterno, al contrario ad esempio dello shuttle, dove la pancia è rivestita da circa 30.000 piastrelle sostanzialmente incollate alla struttura, il che implica azioni molto lunghe e complesse di verifica e manutenzione tra un volo e l’altro: parliamo di milioni di ore/uomo. Nel nostro caso abbiamo pannelli 50×30 centimetri, molto più grandi delle piastrelle usate per lo shuttle, più grandi addirittura delle piastrelle che rivestono i nostri pavimenti. Questo significa che ne servono molte di meno. Inoltre, senza toccare le guarnizioni, con una chiave inglese ed un cacciavite, dall’esterno si tolgono senza problemi. Con il cacciavite si tolgono infatti quattro tappi di un materiale speciale che mantengono la superficie esterna completamente piatta e uniforme, al di sotto dei quali ci sono quattro bulloni, uno per tappo; tolti questi ultimi il pannello viene via senza problemi, e altrettanto facilmente si rimette. Grazie al tappo evitiamo qualsiasi modifica al flusso aerodinamico e la generazione di relativi punti più caldi rispetto al resto della superficie.
Oltre a questo vantaggio che riguarda la facilità di verifica e manutenzione dei pannelli, un altro è dovuto al fatto che la nostra è una struttura calda. In altre parole, al posto del concetto classico alla base dello shuttle, del Buran e dell’Hermes, dove c’era una struttura interna portante, fredda, ed una struttura esterna protettiva e calda, nel nostro caso la funzione strutturale e di isolamento termico sono svolte dagli stessi elementi, con una semplificazione dell’architettura dell’ala, una riduzione delle parti, un maggior spazio interno per i sottosistemi a parità di forma alare e una riduzione dei pesi. (nel disegno, fonte TAS-I, un ipotetico shuttle italiano realizzato con le tecnologie ora sperimentate)
Come sono realizzati i vostri “piastrelloni”?
Con un sandwich ceramico piuttosto complicato, con due “pelli” esterne ceramiche e un core interno in schiuma ceramica, che aumenta enormemente l’inerzia termica. La funzione isolante che abbiamo potuto misurare è assolutamente sorprendente: in uno spessore molto contenuto, di appena due centimetri, si riesce ad abbattere drasticamente il gradiente termico, mantenendo l’interno a temperature assolutamente sopportabili per una qualsiasi elettronica odierna. Sui pannelli, dalla parte esterna, viene poi depositato superficialmente del carburo di silicio per evitare fenomeni ossidativi.
È riutilizzabile come le piastrelle dello shuttle?
Si. Quello che abbiamo sottoposto a test è praticamente come nuovo. Ne siamo estremamente soddisfatti e dobbiamo ricordare che è stato ideato dal dipartimento di ingegneria aeronautica e aerospaziale della Scuola di Ingegneria Spaziale dell’Università “La Sapienza” di Roma, cosa che ci fa piacere perché abbiamo lavorato benissimo assieme, traendo da questa collaborazione un evidente e grande vantaggio. È un segno di come la Scuola, fondata da Broglio, continui a produrre frutti straordinari.
Quindi, rispetto alle piastrelle dello shuttle “erte” una decina di centimetri, siete riusciti ad ottenere le stesse prestazioni riducendo in pratica lo spessore di un quinto?
Non solo. Senza voler togliere nulla allo shuttle, che era un miracolo di ingegneria per i suoi tempi, usando processi tutti sviluppati in Italia e tecnologie già disponibili, ma mai usate prima nel nostro Paese, siamo riusciti a creare qualcosa che prima non c’era.
Possiamo dire che non esiste al mondo un pannello con queste caratteristiche?
Si, è lo stato dell’arte. Ed anche al sistema di refrigerazione attiva, per il momento stiamo puntando solo noi e gli americani.
Le tecnologie messe a punto e ora sperimentate, possono essere usate oltre che per il bordo di attacco alare anche per la pancia dei futuri veicoli aerospaziali?
Si, perché le tecnologie sviluppate sono diverse, e poi assemblate in un unico test article, non perché debbano fisicamente coesistere a così breve distanza, ma per sperimentare al massimo possibile in una sola volta.
Il rivestimento termico dello shuttle presentava una follia ingegneristica, costituito com’era da 30.000 piastrelle ciascuna diversa dall’altra per seguire la forma della pancia. I vostri “piastrelloni” sono più facili da modellare in funzione di qualsiasi forma necessaria alle varie tipologie di veicolo su cui potrebbero essere montate?
Sono fatte con uno stampo, quindi non ci sono problemi a modellarle come si vuole. Anche per il bordo di attacco alare refrigerato non vedo particolari problemi.
A proposito del bordo di attacco alare, è fatto anche questo di materiali ceramici?
No. Forse sarà una sorpresa, ma non è fatto di acciai ad alta resistenza o strani materiali esotici, ma è di semplice alluminio, che ha esaltato le capacità di refrigerazione. In realtà eravamo partiti pensando a materiali speciali, ma ci siamo accorti che l’alluminio era meglio, sia dal punto di vista dei pesi che della capacità di far funzionare la refrigerazione. Con l’Inconel (acciaio ad alta resistenza a base di Nichel, NdR) avevamo invece delle macchie in corrispondenza dei canali di refrigerazione, che davano luogo a strisce fredde alternate. Ciò non toglie che nei prossimi test sperimenteremo anche un pannello in metal matrix avanzato e uno in ceramiche resistenti ad altissime temperature (UHTC), fatti il primo dal CSM (Centro Studi Materiali), capace di superare i mille gradi di temperatura, anche questo un grosso risultato ed una prima mondiale, ed il secondo fatto dal CIRA con il supporto del CNR-ISTEC.
Un’altra caratteristica del sistema sono le strutture a deformazione controllata. Cosa sono?
Nel sistema si doveva far convivere parti insensibili al campo termico con altre che si deformano tantissimo. Riuscirci è stato una sfida vinta con le strutture a deformazione controllata che assorbono con la loro deformazione forze che altrimenti sarebbero enormi. Tutto ha funzionato alla perfezione e non abbiamo avuto nessuno spray di plasma all’interno. Per deformazione controllata si intende che non si progetta più una struttura solo come una sorta di reticolo immobile che deve reggere i carichi, ma come qualcosa che in realtà di muove come un meccanismo che consente alla fine di mantenere la forma esterna sempre invariata per scopi aerodinamici, e nello stesso tempo alle varie parti di dilatarsi quanto serve senza arrivare a stati di sollecitazione che porterebbero a rottura dei singoli componenti. Il controllo non è attivo, ma studiato in fase di progettazione prevedendo esattamente gli sforzi che arriveranno con un modello matematico. Proprio la messa a punto di questo modello matematico è una ricaduta non prevista del nostro lavoro.
Di che si tratta?
Normalmente c’è un percorso che passa da un’analisi esclusivamente strutturale ad una esclusivamente termica, fatte con strumenti e modelli diversi. I risultati dell’analisi termica vengono poi riversati su quella strutturale e se ne vedono gli effetti, che si sommano a quelli ottenuti dall’analisi strutturale vera e propria. In casi di forti gradienti termici e disomogeneità di comportamento, come quello che stiamo considerando, questo approccio classico è penalizzate dal punto di vista dei tempi. Noi siamo riusciti ad avere un modello matematico unico, termico e strutturale insieme, che descrive tutte le non linearità integrando i risultati. In questo modo abbiamo ridotto molto i tempi e ci siamo avvicinati alla realtà virtuale, cioè alla capacità di progettare un pezzo con sempre meno test, che portano via tempo e sono molto costosi. Questo modello che abbiamo messo a punto va bene per la progettazione di qualsiasi tipo di aeromobile.
Come pensate di “rivendere” in ESA o negli Stati Uniti questi risultati?
In ESA stiamo facendo un’attività di promozione attraverso l’ASI, che ha investito molto in questo programma. Del resto, se l’ESA vuole fare una sua capsula, siamo ben messi, perché siamo gli unici che hanno testato qualcosa. EADS ha alcune singole tecnologie, ma non ha mai testato un sistema integrato come il nostro. Riguardo potenziali interessi degli americani o dei russi, non saprei, perché entra in gioco anche un aspetto politico. Quello che è certo è che negli USA il volo ipersonico è tornato uno dei temi principali di ricerca.
Ricordiamo ai nostri lettori non tecnici che con “multi-fisico” si vuole intendere l’affrontare un problema reale così com’è, cioè senza separare i vari aspetti meccanico, termico, elettrico, ecc., ma considerandoli nel loro insieme
Per “Non lineare” si intende il comportamento di alcune strutture che a fronte di un carico crescente non si deformano in modo altrettanto omogeneamente crescente, ma una “a salti”.
Fonte: dedalonews.it
Ove non diversamente indicato, questo articolo è © 2006-2025 Associazione ISAA - Leggi la licenza. La nostra licenza non si applica agli eventuali contenuti di terze parti presenti in questo articolo, che rimangono soggetti alle condizioni del rispettivo detentore dei diritti.